The Essential Role of Automotive Connecting Rods Manufacturers
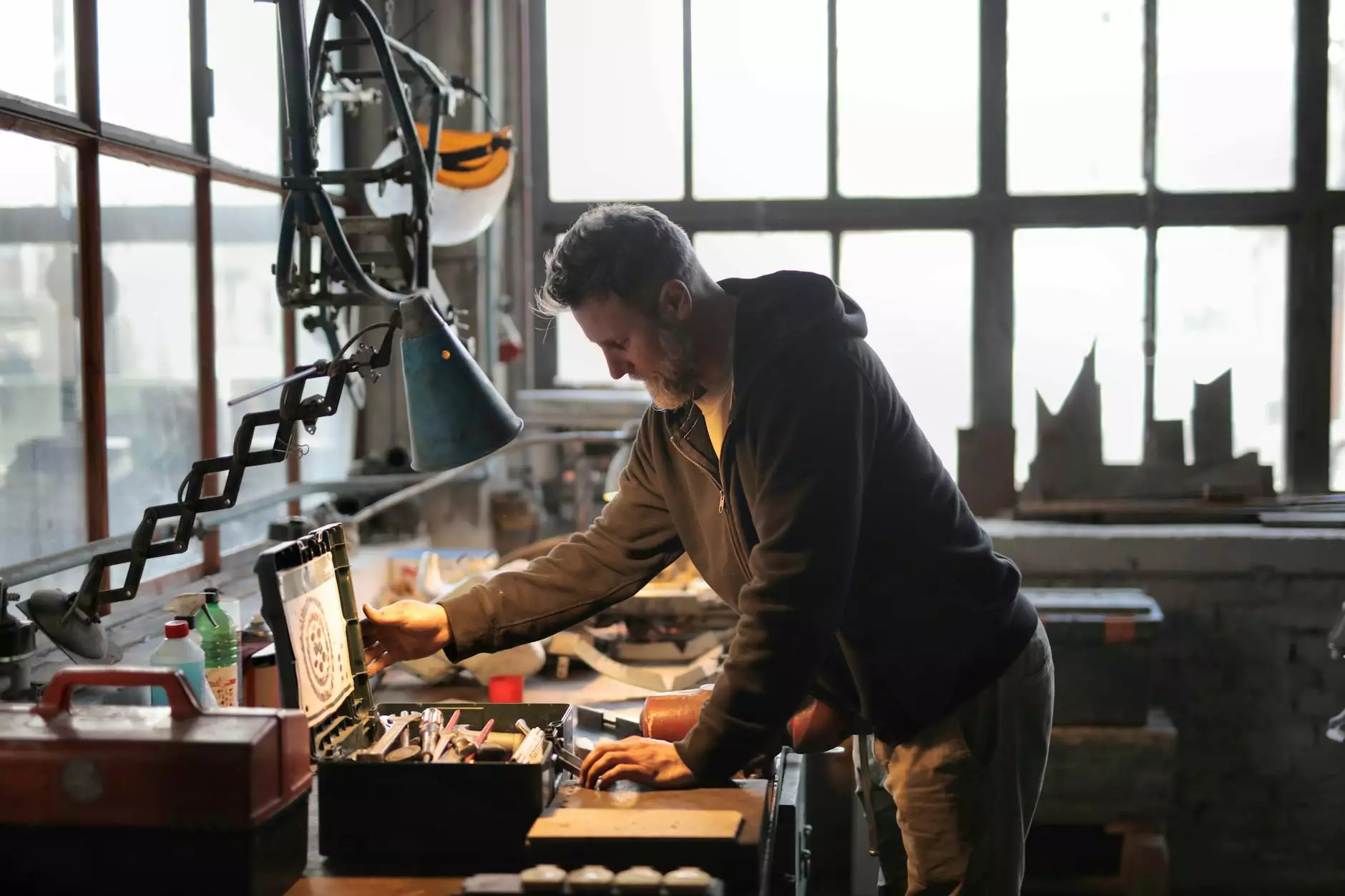
The automotive industry plays a crucial role in modern transportation, encompassing a myriad of parts and components that work in unison to ensure vehicles operate seamlessly. Among these components, automotive connecting rods stand out as a critical element in engine performance. Understanding the importance of automotive connecting rods manufacturers is vital for anyone seeking to delve deeper into the complexities of engine mechanisms and diesel engine parts.
What are Connecting Rods?
Connecting rods are essential components of an internal combustion engine. They serve the purpose of linking the piston to the crankshaft, converting the linear motion of the piston into rotational motion needed to turn the crankshaft. This action is integral to the engine's power delivery system. The efficiency and reliability of this motion greatly rely on the quality and design provided by automotive connecting rods manufacturers.
Types of Connecting Rods
Connecting rods vary significantly based on their design, material, and application. Here are some common types:
- Steel Connecting Rods: Known for their strength and durability, these rods are widely used in high-performance engines.
- Aluminum Connecting Rods: Lighter than steel, aluminum rods are popular in racing applications where weight savings are crucial.
- Forged Connecting Rods: Manufactured through a forging process, these rods offer enhanced strength and reliability.
- Cast Connecting Rods: While less expensive, cast rods are generally used in lower-performance applications.
The Manufacturing Process
The manufacturing process of connecting rods is intricate and requires precision engineering. Here’s a brief overview of the steps involved:
- Material Selection: Manufacturers choose materials based on the intended application and performance requirements.
- Forging or Casting: Most connecting rods are either forged or cast. Forging provides higher strength, while casting can be more cost-effective.
- Machining: Post-forging or casting, connecting rods undergo machining to achieve precise dimensions and tolerances.
- Heat Treatment: This process enhances the material properties, increasing strength and resistance to fatigue.
- Inspection: Rigorous quality control checkpoints ensure that the connecting rods meet the highest industry standards.
The Role of Automotive Connecting Rods Manufacturers
Automotive connecting rods manufacturers are at the forefront of innovation in engine design and efficiency. They provide components not just for conventional gasoline engines but increasingly for diesel engines as well, which demand specific qualities due to their operating characteristics.
Quality Assurance
Manufacturers emphasize quality assurance processes to guarantee that each connecting rod can withstand the intense conditions within an engine. Features of quality assurance include:
- Material Testing: Each batch of material undergoes rigorous testing to ensure it meets strength and performance criteria.
- Dimensional Accuracy: CNC machines are often employed to achieve tight tolerances.
- Fatigue Testing: Connecting rods are subjected to simulated loads to assess their durability over time.
Innovation and Technology
With the rise of advanced technologies, automotive connecting rods manufacturers are continually evolving. Modern manufacturing techniques, such as:
- Additive Manufacturing: 3D printing is creating opportunities for custom components that were previously unattainable.
- Computational Design: Using computer simulations to optimize the design before production helps yield better performance results.
- Smart Materials: The exploration of new materials that offer enhanced performance benefits is on the rise.
The Impact of Connecting Rod Quality on Diesel Engines
In diesel engines, connecting rods must endure extreme stress due to high compression rates. Thus, the role of automotive connecting rods manufacturers becomes even more pivotal. The quality of these components directly influences:
- Performance: High-quality rods optimize power transfer and efficiency.
- Durability: The longevity of an engine is heavily reliant on the resistance of connecting rods to wear and deformation.
- Fuel Efficiency: Well-engineered connecting rods contribute to reduced friction, enhancing fuel efficiency.
Choosing the Right Manufacturer
Choosing the right automotive connecting rods manufacturer is crucial for anyone involved in engine manufacturing or repairs. Here are some tips:
- Experience: Select manufacturers with a proven track record in producing high-quality components.
- Reputation: Research customer reviews and industry reputation to gain insight into the reliability of their products.
- Technical Support: Look for manufacturers that offer robust technical support and expertise.
- Compliance Certifications: Ensure that manufacturers comply with industry standards and certifications.
Conclusion
In conclusion, the importance of automotive connecting rods manufacturers cannot be overstated. As the engine components that contribute significantly to performance and reliability, connecting rods must be crafted with precision and care. Engaging with reputable manufacturers not only ensures high-quality parts but also enhances the overall efficiency of diesel engines and vehicles at large. By understanding the intricate details of connecting rod manufacturing and the role these elements play in the automotive industry, stakeholders can make more informed decisions that ultimately lead to superior engine performance.
Additional Resources
For those who wish to educate themselves further about automotive parts and manufacturing processes, consider exploring the following resources:
- Client Diesel - Diesel Engine Parts
- Client Diesel - Spare Parts Suppliers
- Client Diesel - Blog