The Importance of Oil Seal Factories in Diesel Engine Parts Production
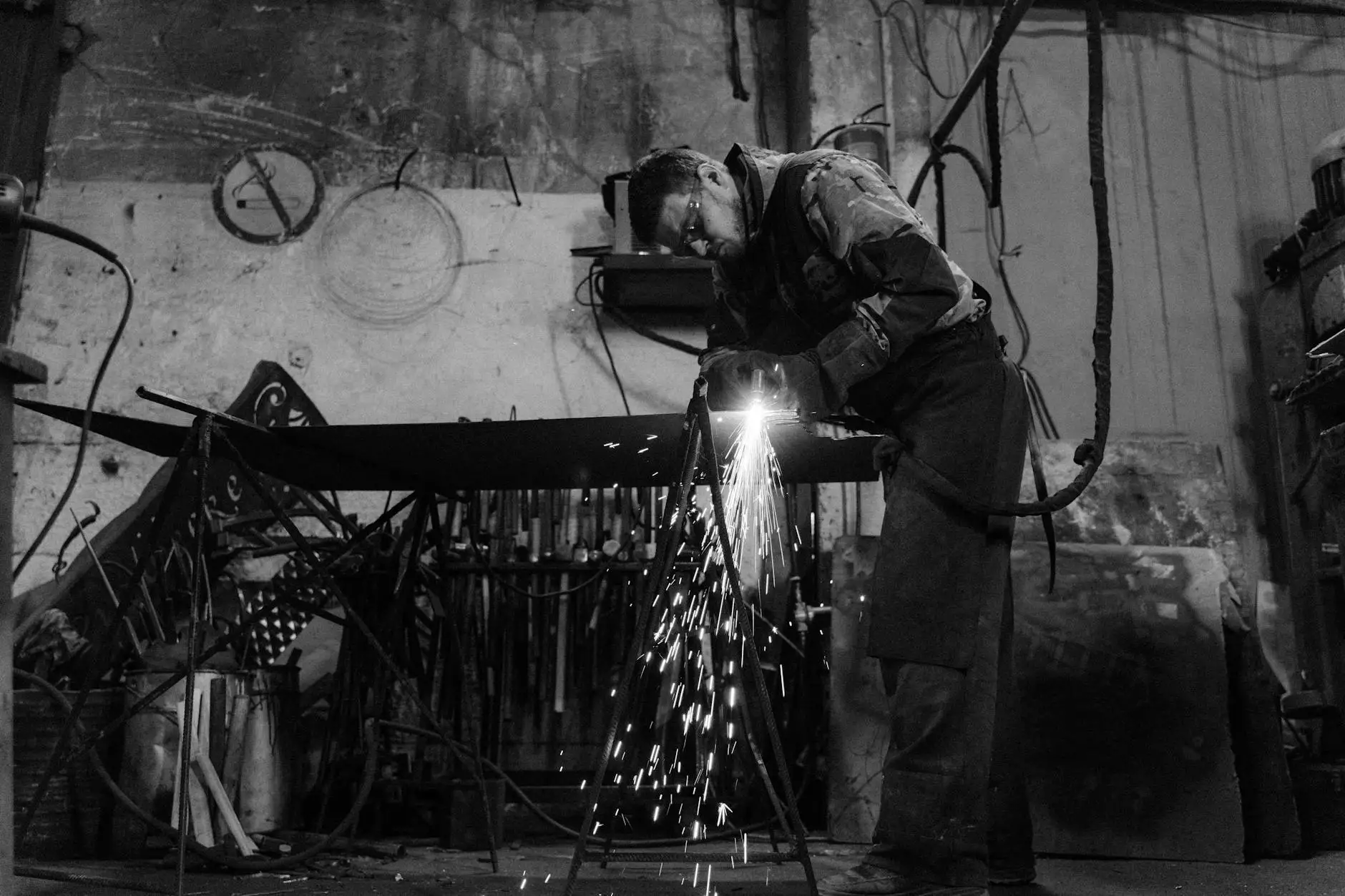
The automotive industry has a profound impact on global commerce, with diesel engines powering a large segment of vehicles and industrial machinery. At the heart of these engines lie essential components that ensure their performance and longevity, such as oil seals. An oil seal factory plays a crucial role in producing these vital components, contributing significantly to the overall functionality and reliability of diesel engines. This article delves into the essentials of oil seal factories, the manufacturing processes involved, and the benefits of sourcing spare parts from reputable suppliers like client-diesel.com.
What Are Oil Seals and Their Significance?
Oil seals, also known as shaft seals, are critical components used in engines and machinery to prevent the leakage of fluids, such as oil or grease, from the engine compartments. They also inhibit the entry of dirt and contaminants, which can adversely affect engine performance. This is especially crucial in diesel engines, where even minor leaks can lead to significant operational issues.
Functions of Oil Seals
- Preventing Fluid Leakage: Oil seals create a tight seal around the rotating shafts to prevent the escape of lubricants, ensuring the engine runs smoothly.
- Contaminant Protection: By sealing off engine compartments, they protect against dirt and debris that can cause wear and tear.
- Enhancing Efficiency: Properly functioning oil seals aid in maintaining optimal oil pressure, contributing to improved engine efficiency.
The Manufacturing Process of Oil Seals
The process of fabricating oil seals is intricate and requires strict adherence to industry standards to ensure high quality. Oil seal factories utilize various materials, including rubber, silicone, and polymers, to manufacture seals suitable for different applications.
1. Material Selection
The first step in the manufacturing process involves selecting appropriate materials. Common choices include:
- Rubber: Known for its excellent sealing properties and flexibility.
- Silicone: Highly resistant to temperature variations, ideal for extreme conditions.
- Polymer Composites: Hybrid materials that offer enhanced durability and performance.
2. Design and Mold Creation
Once the materials are chosen, engineers design the oil seals and create molds. This is a crucial step as precision in the mold design directly affects the final product's fit and function.
3. Manufacturing Process
The actual manufacturing process often involves the following methods:
- Injection Molding: A common technique where heated material is injected into molds to form oil seals.
- Compression Molding: Involves placing raw material into a heated mold to form the desired shape.
- Extrusion: Useful for creating oil seals with specific cross-sectional profiles.
4. Quality Control
After manufacturing, the seals undergo rigorous testing to ensure they meet quality and durability standards. This may include:
- Leak Testing: Ensuring no fluid can escape through the seals.
- Dimensional Check: Verifying that the seals fit precisely as per specifications.
- Material Testing: Assessing the seals' resistance to oil, heat, and wear.
Importance of Sourcing from Reliable Oil Seal Factories
When it comes to spare parts suppliers for diesel engines, choosing a reputable oil seal factory is paramount. Here’s why:
1. Quality Assurance
Reputable manufacturers like client-diesel.com are committed to quality. They adhere to international standards and certifications, ensuring that each oil seal produced meets the highest benchmarks in the industry.
2. Customization Options
Established oil seal factories often offer customization possibilities. They can design and manufacture seals tailored to unique specifications, accommodating various engine designs and applications.
3. Cutting-Edge Technology
Advanced manufacturing technologies enable factories to produce oil seals that are not only precise but also durable and long-lasting. Investing in state-of-the-art equipment and processes results in superior product performance.
4. Technical Support and Consultation
Working with professional oil seal manufacturers often comes with added benefits such as expert consultation and technical support to ensure you choose the right seals for your needs.
How to Choose the Right Oil Seal Factory
- Research the Reputation: Look for reviews and testimonials from other customers.
- Evaluate Product Range: A factory that offers a diverse range of products is more likely to meet varied needs.
- Check for Certifications: Ensure the factory complies with recognized industry standards.
- Assess Customer Service: Good communication and support from the manufacturer can facilitate better service.
The Future of Oil Seal Manufacturing
The automotive industry is continually evolving, and so is the manufacturing of oil seals. Recent trends indicate a shift towards sustainable practices and materials in the production processes. Oil seal factories are exploring eco-friendly alternatives aimed at reducing waste and environmental impact.
Emerging Technologies
Advancements in manufacturing technology, such as 3D printing, are set to revolutionize production processes, enabling rapid prototyping and on-demand manufacturing of custom seals. This innovation opens avenues for improved supply chain efficiency and reduced lead times.
Integration of IoT in Manufacturing
The integration of Internet of Things (IoT) technologies within manufacturing facilities promises to enhance operational efficiency. Smart manufacturing systems could analyze production data in real-time, facilitating proactive maintenance and quality control.
Conclusion
In conclusion, oil seals are an indispensable part of diesel engines and machinery, and the significance of oil seal factories cannot be overstated. By understanding the manufacturing processes, the importance of quality, and future trends, businesses can make informed decisions when sourcing their engine parts. Relying on trusted suppliers like client-diesel.com ensures access to high-quality spare parts that enhance the performance and longevity of diesel engines. As the industry continues to advance, the role of oil seal factories will remain crucial in ensuring that engines operate efficiently and sustainably.
FAQs About Oil Seals
1. What materials are used to make oil seals?
Oil seals are generally made from materials like rubber, silicone, and polymer composites depending on the application needs.
2. How can I tell if my oil seal is failing?
Signs of a failing oil seal can include engine oil leaks, increased engine noise, and a decrease in engine performance.
3. Can oil seals be replaced, and how often should they be checked?
Yes, oil seals can be replaced. They should be inspected regularly as part of routine engine maintenance, typically during oil changes or significant service intervals.
4. Where can I find reliable oil seal suppliers?
It's best to look for suppliers with a strong reputation, industry certifications, and a good track record of quality, such as client-diesel.com.